Setbacks
This week we returned to working on the parachute system. With the new receiver, we were able to set up the release servo motors. After some testing, we realized that the servos we originally planned to use did not fit our specifications. Fortunately, we were able to repurpose some other servos we had on hand.
We then spent the next few days setting up the release mechanism arms. We modeled and then printed multiple parts before finally settling on a design that worked. At this point, we were ready to test the parachute system for the first time. This test would inform us if the parachute performed as expected. The two objectives of this test were to determine if the parachute system was strong enough to withstand the force of the springs when fully compressed and to test if the springs were strong enough to launch the parachutes.
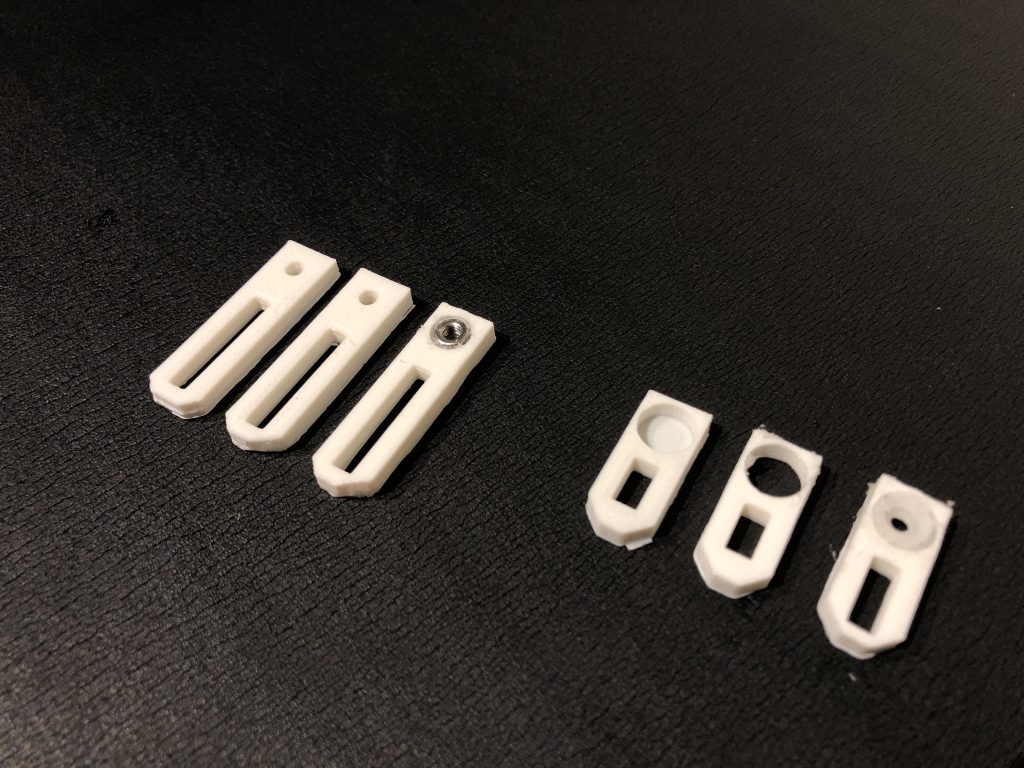
The second objective was the most critical as we have had multiple problems with spring strength before (more about this here). After weeks of designing, multiple failed prints, a dead receiver and much more, it all came down to one test. Success would mean passing one of the biggest obstacles in the way to our test flight. The consequences of failure could be devastating causing any where from a few days to weeks of work to fix the issue. Finally we were ready.
To say it did not go well would be a understatement. The parachute did not even clear the tube. After a few more tests were performed to determine if it had been a fluke, we were forced to confront the results. The parachute system was massively under powered. Our next step was to determine the cause of the issue by performing more tests. Some of these tests involved packing the parachute tighter to check if it was causing friction while being launched and drilling holes in the side of the tube to test if increased air flow would help. Neither of these tests were successful. This meant that the problem was most likely caused by the springs.
These tests also revealed another problem. The hinges that attached the lid to the tube were beginning to show signs of breaking. The parachute system had almost simultaneously failed both parts of the test.
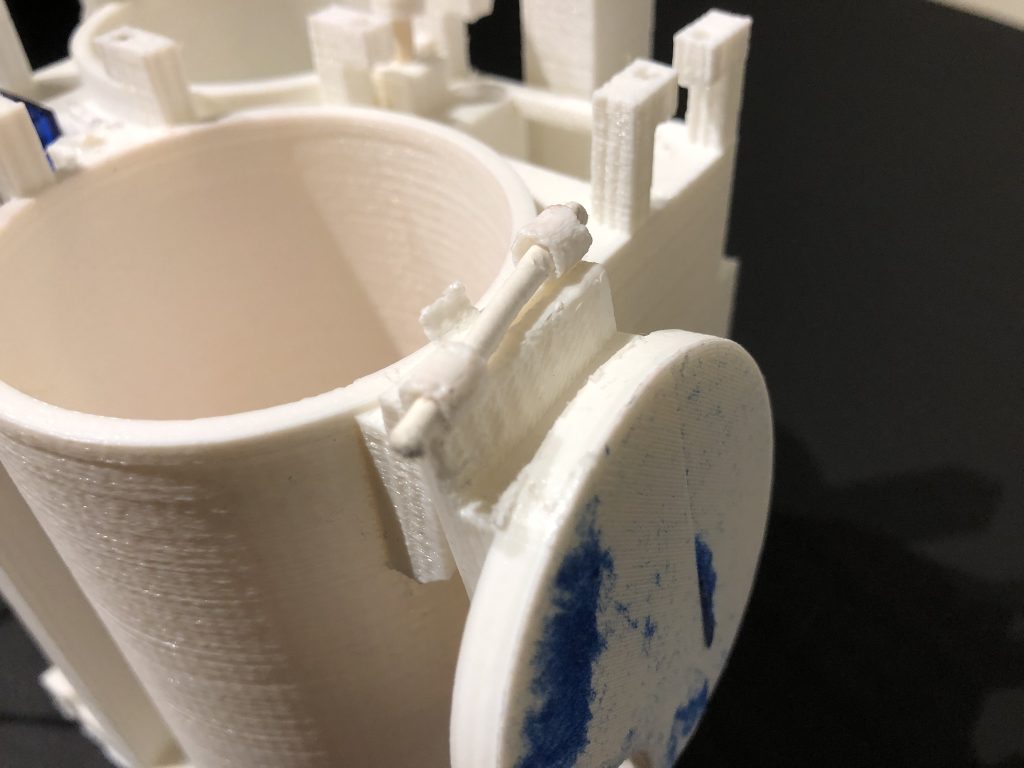
To fix the spring problem, we could increase the strength of the springs but this would cause two new problems: The more powerful springs would put even more stress on the parachute system witch was already failing. Also one of our design requirements is for the parachute system to be packable by hand, a criteria we are barely meeting with our current springs.
The fix for the failing hinges is simpler but time consuming. This fix would involve increasing the size and strength of the hinges and then printing a new parachute system, a process which will take a few days to complete. Unfortunately, this would only make a small part of the parachute system more durable. Installing more powerful springs would only reveal more weak spots.
Our other option is to switch to a different deployment system such as compressed gas or pyrotechnics. While this would most likely have more than enough power to launch the parachutes, changing the deployment method will require a full redesign of the parachute system. At this time, we are considering our options and will post an update when available.
Part two here.